What is Vitreous Enamel?
Vitreous Enamel is a glass surface fused to a steel substrate at very high temperatures - over 800°C.
Our process of application is referred to as wet enamelling. Wet enamelling must be done by hand and is the most skilful type of enamelling. Multiple applications and firings build a number of glass layers with a depth of colour.
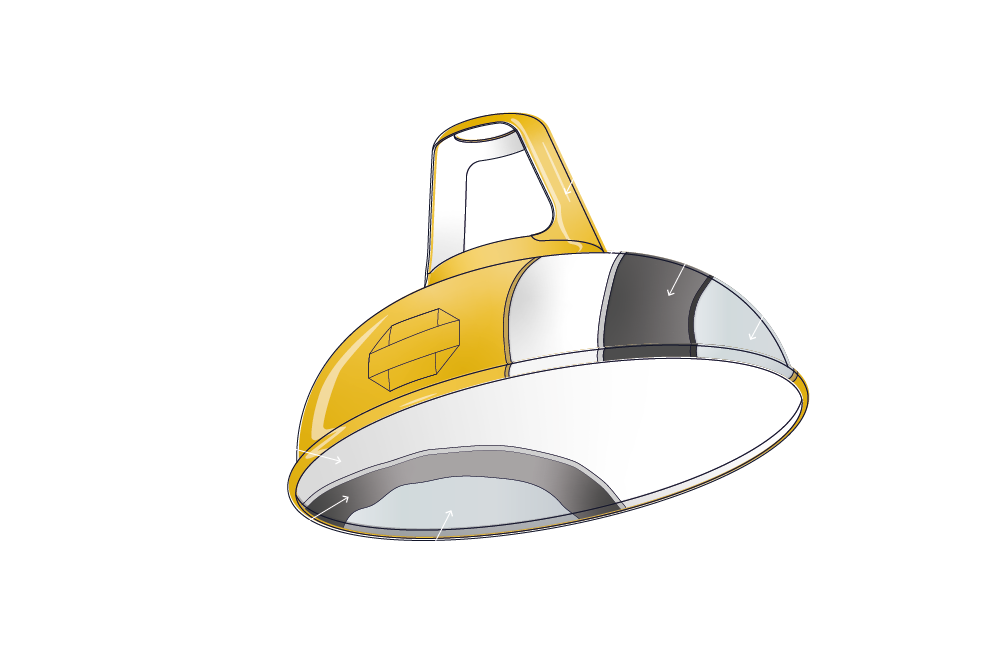
What are the advantages of Vitreous Enamel?
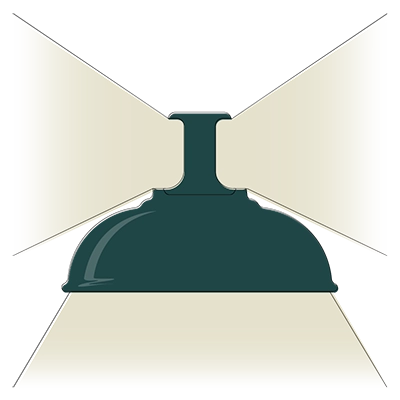
High Efficiency Finish
The glass Vitreous Enamel coating is much more reflective than any paint or powder coating finish. The white enamel inside the lampshade reflects a clean, bright light and is highly efficient at providing task and ambient lighting.
The white enamel colour was selected for its neutrality; it will not add a tint to the lightbulb colour.
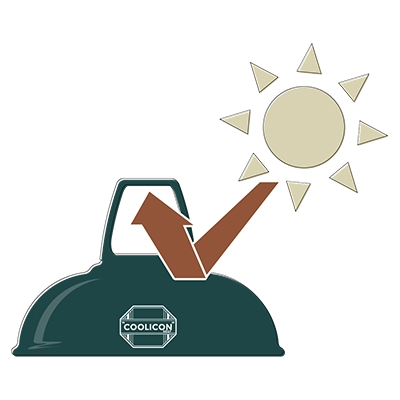
Fade-proof
The colour of a Coolicon® lampshade will remain as rich and vibrant as when the lampshade was first produced. This is because Vitreous Enamel does not fade or discolour. This finish ensures resilience in bright sunny environments such as conservatories, or near south-facing windows.
Top tip: We recommend placing Coolicon lampshades in a bright environment to truly appreciate the depth of colour.
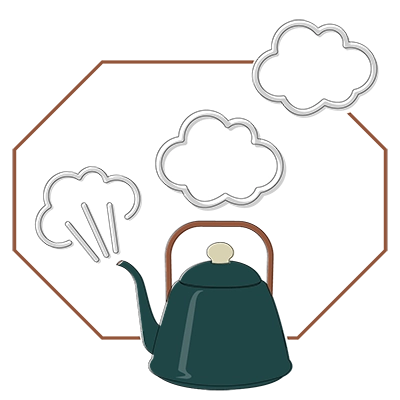
Steam And Corrosion Resistant
Our continuous Vitreous Enamel finish over the whole lampshade ensures durability against steam. This impervious glass finish protects the lampshade in warm, steamy environments such as kitchens. Unlike paint and powder coatings, a Coolicon Lampshade will never rust – the perfect kitchen companion.
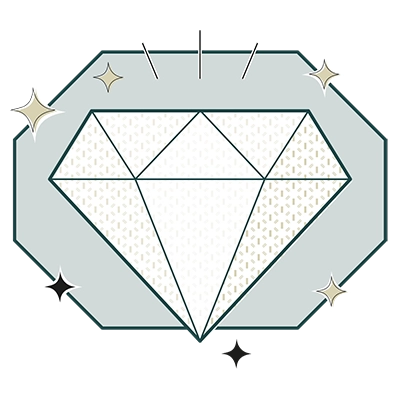
Ultra-tough Finish
The layers of Vitreous Enamel are individually fired, forming a homogeneous durable finish.
The robust glass coating is difficult to scratch and its strength prolongs the lifespan of the lampshade.
Minor chips will not lead to corrosion or compromise the safety of the lampshade.
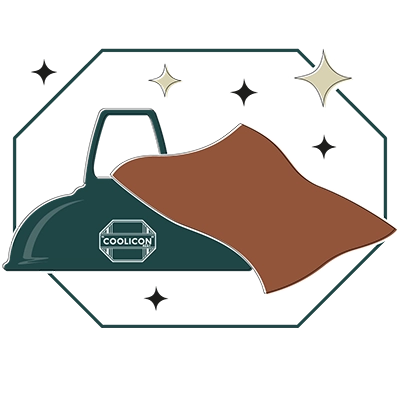
Easy To Clean
Due to the continued, seamless finish the lampshade can easily be cleaned with a soft cloth.
For stubborn marks a high-quality window/glass cleaner can be applied to the cloth and passed over the lampshade. Care should always be taken to avoid contact with the Coolicon badge.
Important: The lampshade should only be cleaned when the light switch is off and there is no power to the circuit. It is important that the electrical fitting is not exposed to any liquids.
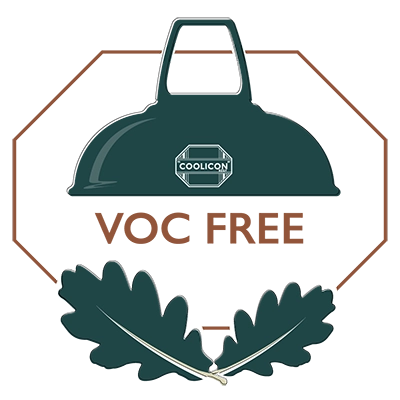
Healthy To Live With
Vitreous Enamel is mainly composed of glass, with natural minerals and oxides fused into it. Glass is an impermeable material; it is non-VOC (volatile organic compound) and will not emit any gases or react with chemicals.
In comparison, painted and powder-coated products are reliant on petrochemical-based paints.
There are no harmful chemicals used in the production of Coolicon Lighting products or packaging. Our packaging is printed using water-based inks, contains no polystyrene and is composed of recyclable cardboard. Where possible, packaging weight is kept to a minimum to reduce fuel usage during transit.
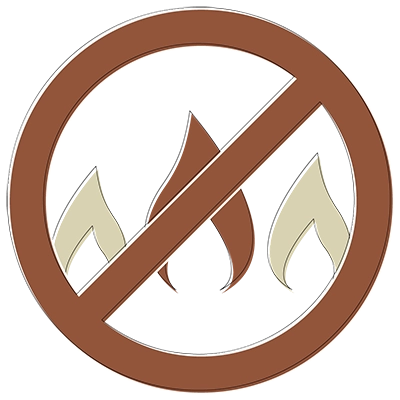
Fire Safe
Fired at over 800°C during the production process, our lampshades are non-flammable and are able to withstand an extreme amount of heat without becoming a fire risk.
15 steps, over 3 days
Day 1
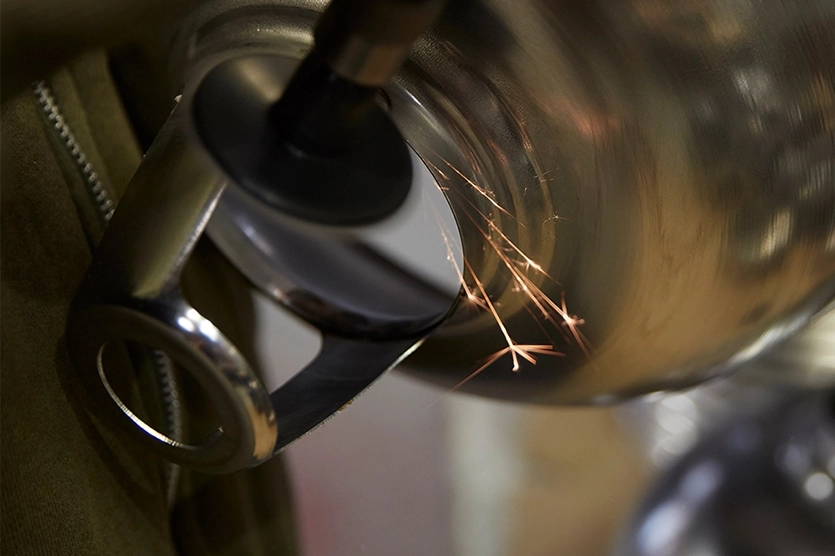
1. Weld Chasing
When the steel lampshade arrives at the enamel factory any welding or forming marks are carefully removed by hand.
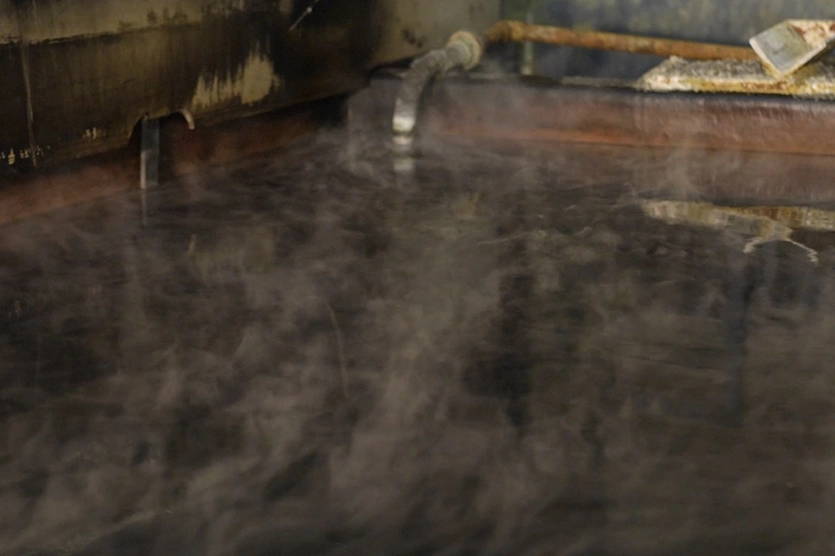
2. Etching
After being prepared, the lampshade is dipped into a series of hot degreasing baths for a quick clean before entering an acid bath. The acid etches the surface of the lampshade, ensuring the Vitreous Enamel ground coat can fuse to the steel surface.
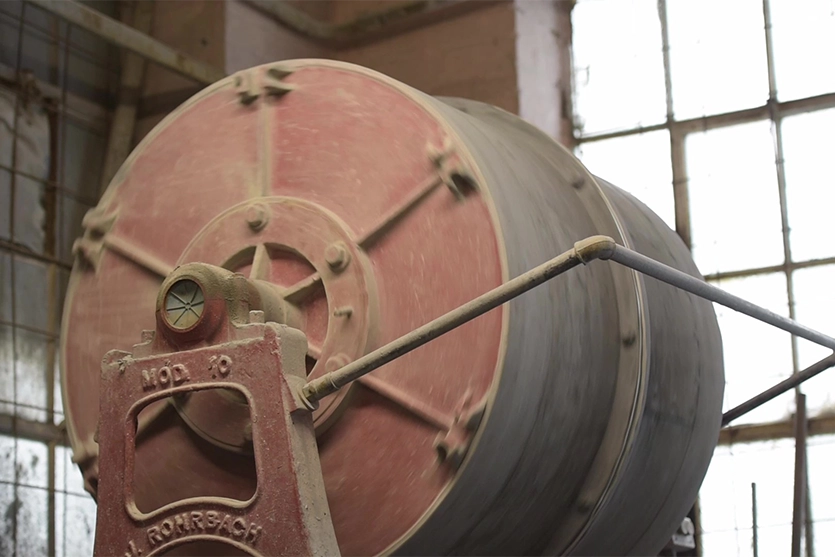
3. Ground Coat Milling
Glass chips and minerals are measured and milled together into a dark liquid to form the enamel ground coat. Milling this coarse undercoat can take up to 8 hours.
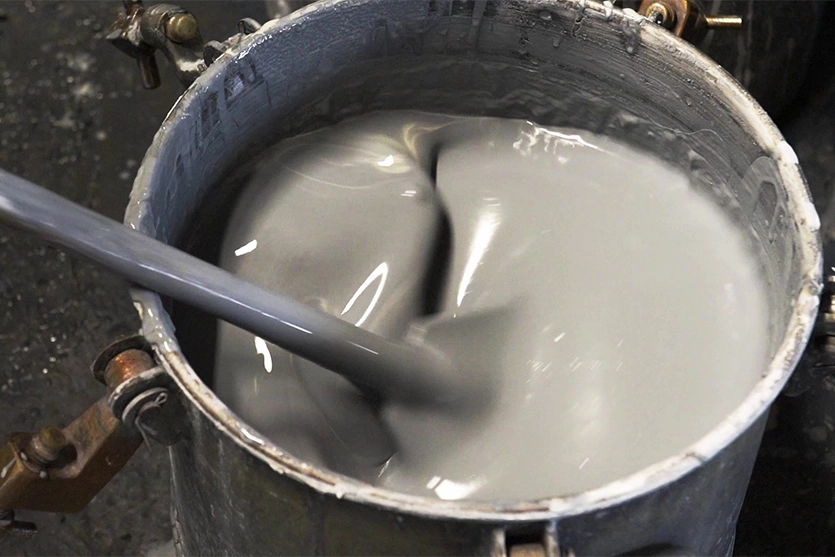
4. Ground Coat Application
The liquid ground coat is then hand sprayed inside and outside the lampshade. The thickness of the ground coat varies depending on what the colour of the lampshade will be.
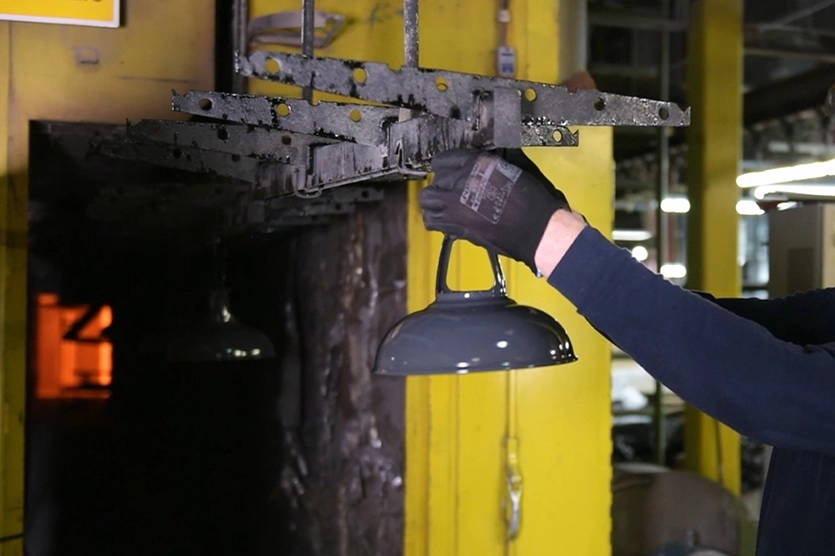
5. First Firing
After letting the ground coat dry, the lampshade enters the 850°C furnace for its first 30-minute firing cycle.
Day 2
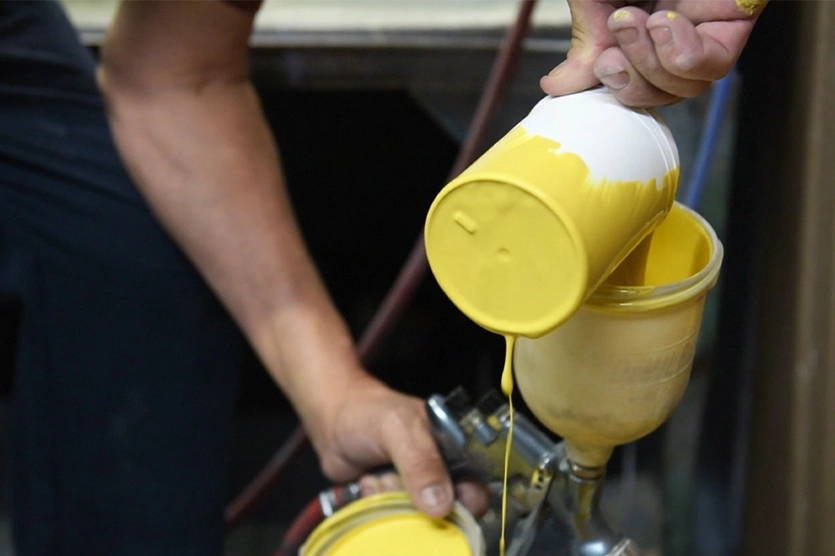
6. Coloured Coat
A secret recipe of natural minerals and oxides are milled together to create the colourful enamel top coat.
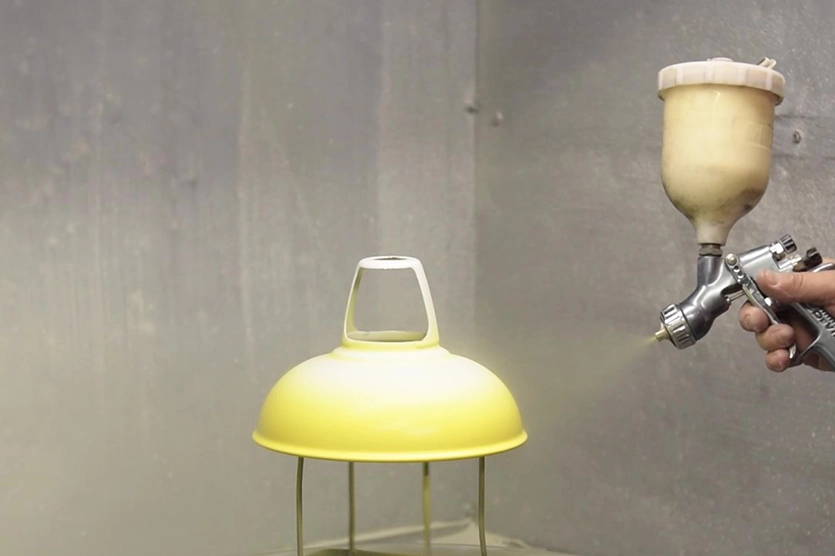
7. Outside Colour Application
The coloured enamel is now applied onto the outside of the lampshade. Some colours, like yellow, need a white coat of enamel before their double colour top coats - this requires extra firings.
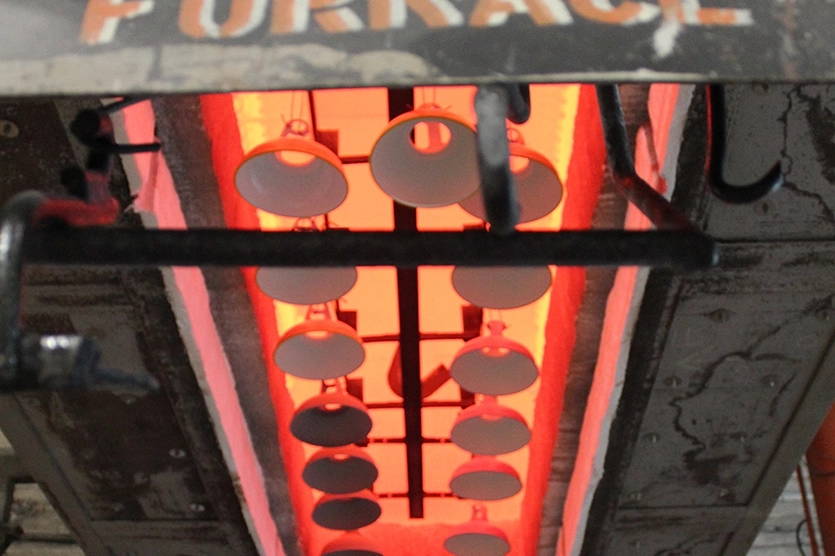
8. Second Firing
The lampshade is then hung to dry before being fired again, this time at around 800°C.
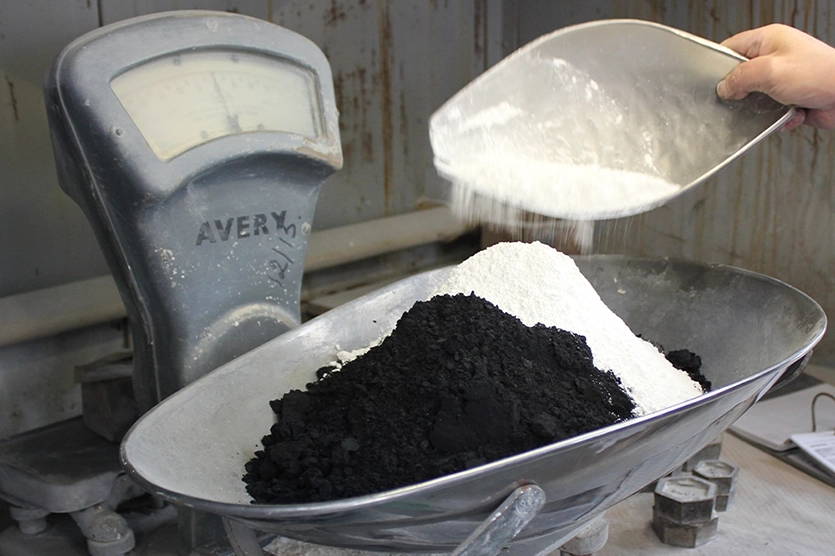
9. Final Coat Oxides
The minerals and oxides for the white Vitreous Enamel inside are measured and then milled into a liquid enamel.
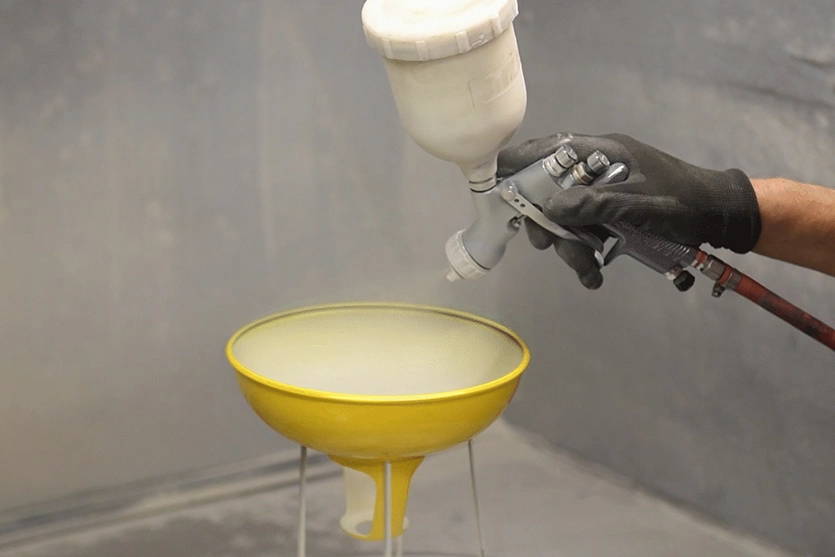
10. Inside Colour Application
The white enamel is applied inside the reflector of the lampshade. Any white sprayed on the outside of the lampshade is left to dry and then wiped off by hand before firing.
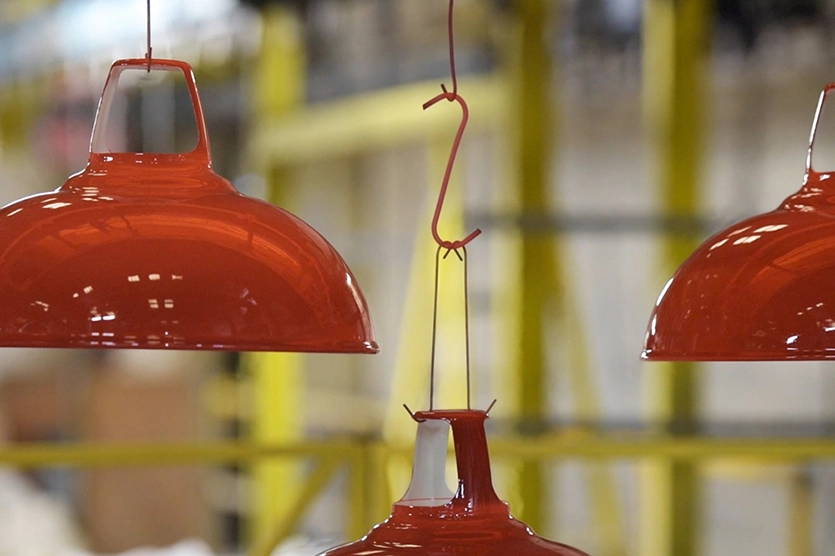
11. Final Firing
The lampshade is fired for the last time at 800°C before cooling prior to inspection.
Day 3
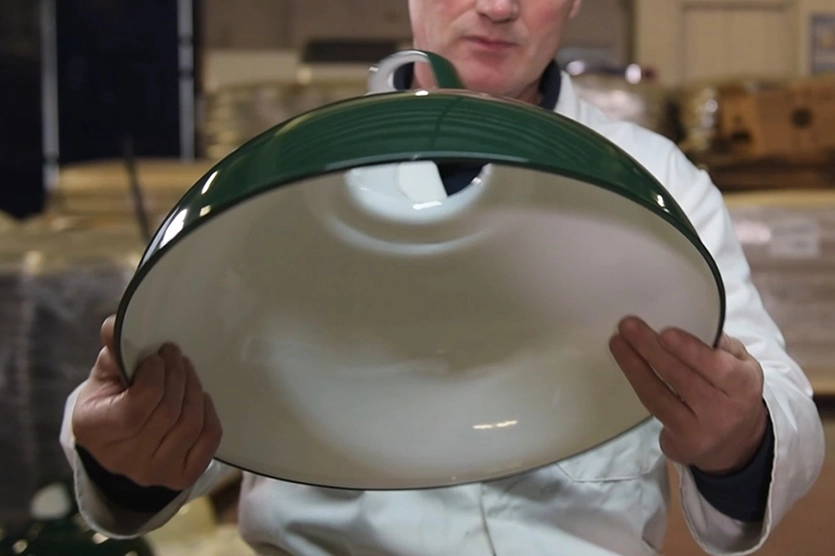
12. Inspection
The enamelled lampshade now passes through quality control where it is closely inspected. Reject lampshades will have their enamel blasted off ready to go through the whole process again.
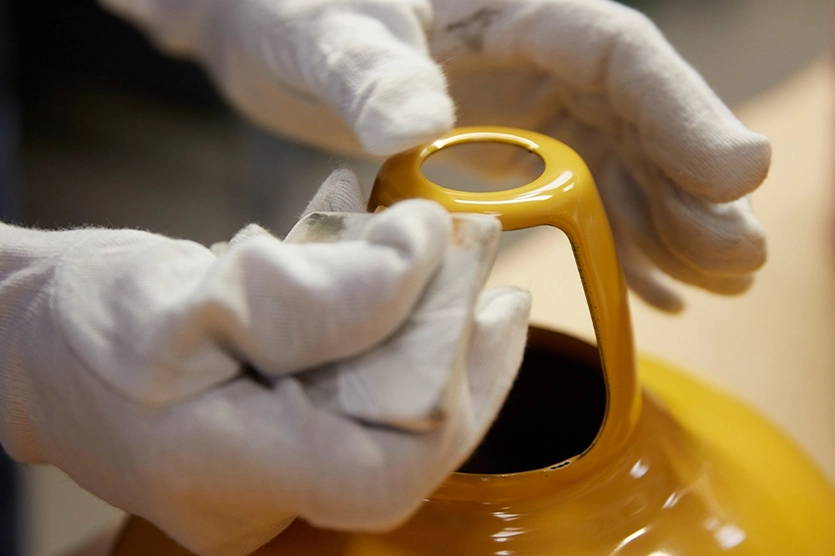
13. Hand Finishing
After inspection, hanging marks are removed by hand with an abrasive stone. Because of this process, every lampshade that passes is perfect in its own unique way.
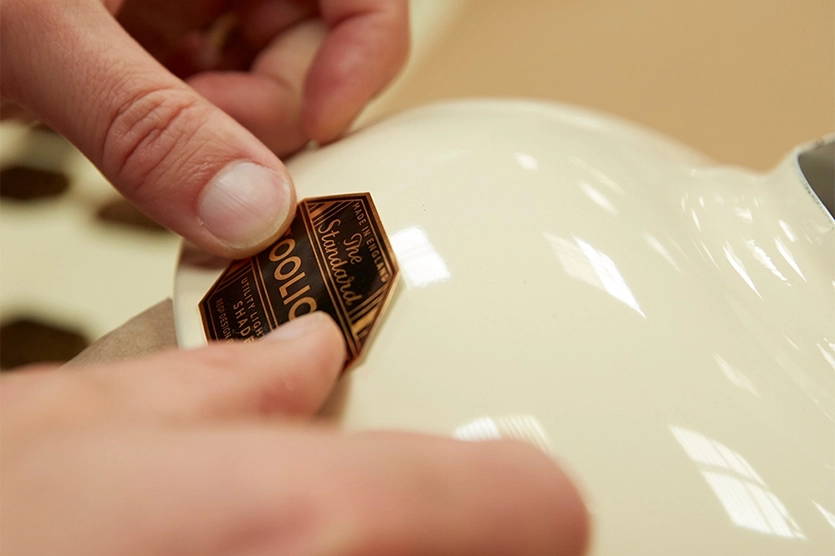
14. Application of the Gold Badge
After passing inspection, the gold Coolicon® badge is hand applied, creating unique creases. The lampshade is now officially a Coolicon Lighting lampshade.
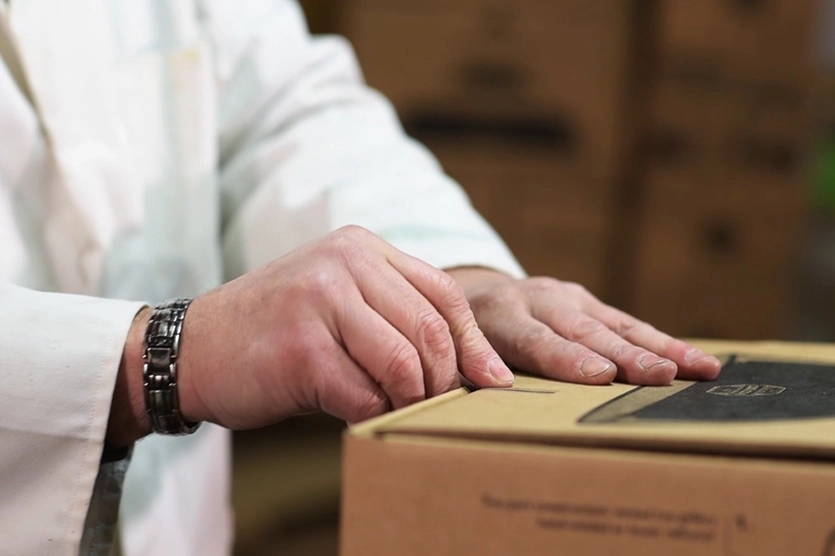
15. Packaging
After a quick clean, the Coolicon Lighting lampshade is carefully packaged and labelled, ready for a new home.
Maker's Marks: The Beauty of Honest Materials and Processes
Made by hand in a down-to-earth factory Coolicon lampshades are crafted by generations of craftspeople and directly reflect the human influence. A process largely unchanged in 100 years, hand enamelling gives our lampshades their unique character marks, or “Maker’s Marks” as we like to call them. Variation in appearance is natural as the enamel melts and flows over the surface of the lampshades in a semi-controlled fashion. Below are some classic Maker’s Marks that can be seen on our lampshades and are, if you spot any, truly unique to your Coolicon shade.
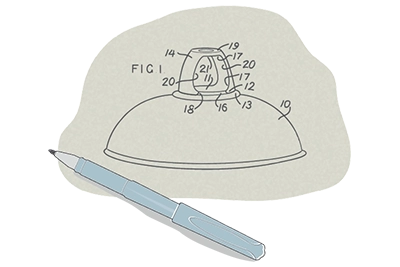
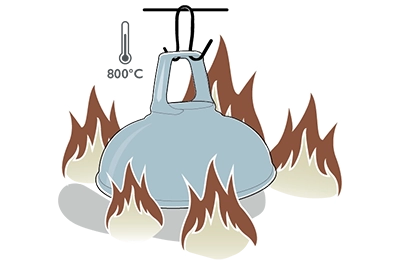
Steel Reflector and Vented Gallery
We use high-grade steel for our 1933™ Design lampshades to ensure they can withstand the 800°C firing temperatures and have the right properties to bond with our Vitreous Enamel finishes.
Spinning, pressing and hand forming create the curved shape of the reflector.
Once perfectly rounded, the reflector is welded to the vented gallery, completing the construction of the contemporary 1933™ Design lampshade.
More often than not, the craftsperson who spins the reflector also welds it to the vented gallery in this two-part process.

The Seal of Approval
After the final inspection, each 1933™ Design lampshade receives its seal of quality – the Coolicon gold badge.
The distinct Coolicon badge continues to be a beacon of quality, just as first applied in 1933. They are still printed on an old-fashioned industrial press before they are expertly aligned by eye and applied by hand.
Any character rich wrinkles are pressed down by the maker and emphasise the lampshade’s curvature.
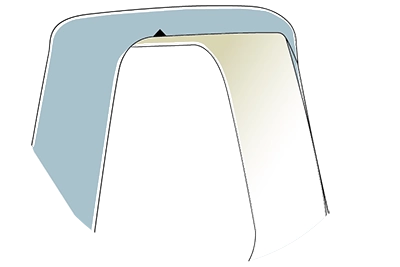
Hanger Impressions
During the enamelling process our lampshades are hung on hangers; as the lampshades journey through the intense heat of the furnaces, the hangers leave impressions in the enamel.
As such, markings around the top of the gallery are completely normal and are an authentic result of the enamelling process.
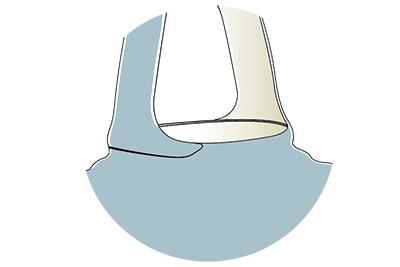
Expressed Edges & Joints
As the enamel melts and flows in the furnace it reveals a beautiful dark edge that contrasts against the bright colours of the lampshade.
Expressed edges can occur around the rim of the lampshade, the gallery and the top joint. This is more prominent on light coloured lampshades and more hidden on darker lampshades.
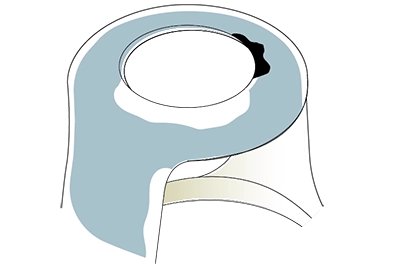
White Edges & Gallery Wick
Sometimes a small amount of white enamel wicks around the edge of the lampshade adding unique character.
During the multiple firings, continued contact with the hooks can wick the colours from one face to the other.
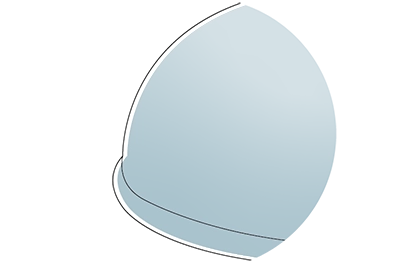
Colour that accentuates forms
As the molten glass flows over the surface of the red-hot steel the enamel pools and thins, this causes slight variation accentuating the contours of the lampshade.
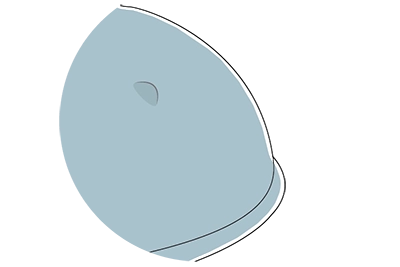
Oxide Bumps
On occasion the enamel may appear inconsistent. If you look closely, you might see tiny dots. These dots are caused by the oxides reacting to the heat of the furnace or by the ground coat being slightly thicker in some areas.
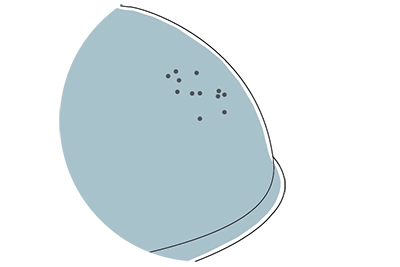
Freckles
Freckles are individual to each lampshade, just like people. They are completely normal and are a part of the enamelling process.